8 Reliability and Maintenance Trends to Watch
By Kevin Clark, former VP, Fluke Reliability
The 2020s are shaping up to be an exciting decade, with massive changes expected to unfold in how maintenance and reliability professionals do their jobs. Here is a look at some trends to watch for.
1. Fewer people are seen on the plant floor
More machines mean a growing concern for worker safety. Increased use of automation and wireless solutions reduces the number of people on the plant floor. While plant-floor jobs start to dwindle, employees will find opportunities in other parts of manufacturing, such as data analysis, artificial intelligence (AI), and more.
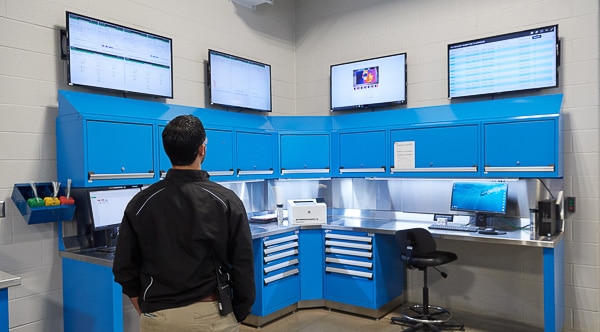
2. Data volumes mushroom
More and more companies will invest in Industrial Internet of Things (IIoT) systems. Maintenance pros leveraging sensors, software, and the cloud to generate asset condition data are guided through maintenance-management decisions. This means increasing volumes of data, which increasingly require AI and machine learning (ML) to help detect patterns and develop insights from the data. Prescriptive maintenance strategies will also let those programs flourish.
3. More machines become connected
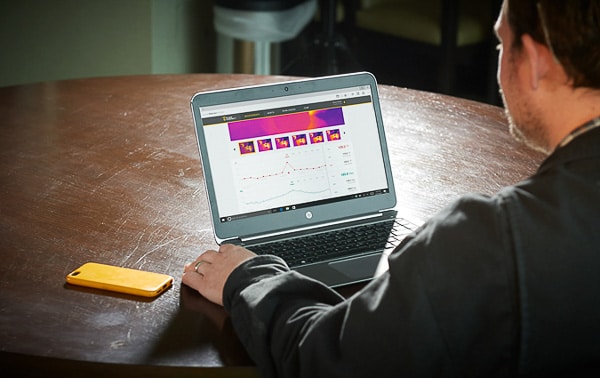
Significantly less than half of all industrial machines are now connected. But as more companies adopt IIoT, we will get closer to the 50% mark. Also, wired systems continue to decline in favor of wireless solutions—though some companies will still remain challenged in upgrading their infrastructure.
4. Reactive maintenance gradually declines:
Companies will continue to strategize about making their maintenance less reactive and wasteful. People are making strides as more companies transition to predictive maintenance. Through technology solutions, the move to predictive maintenance becomes less daunting.
5. Acoustic imaging continues its rise
More companies will recognize the value of leak detection. Acoustic imaging tools greatly simplify the process of leak detection, making it easier for companies to save energy and reduce costs.
6. Augmented reality for maintenance teams
Technicians can see a virtual overlay using augmented reality (AR) devices. Technicians can compare a video with their own repair using a dual view. Or, they can view a repair manual at the same time as they are working on an asset. Expect wearable devices with AR to be in vogue soon.
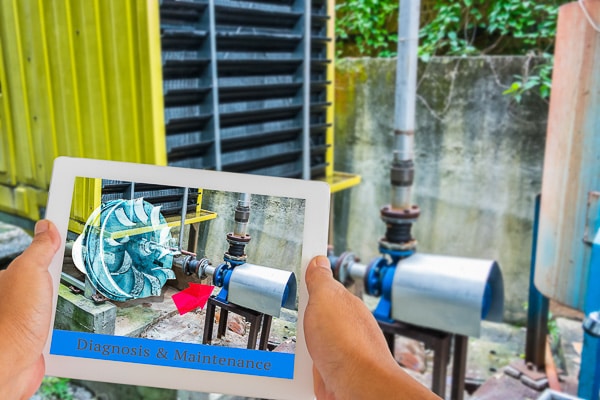
7. Generational shift moves into a higher gear
The tide of baby boomers retiring escalates, with millennials stepping in to fill their shoes. And look out, Gen Z (the generation after millennials) is now joining the workforce. Veteran maintenance pros from all generations who want staying power must improve soft skills. Becoming more digitally savvy is a modern-day demand.
8. Increase in clean energy spurs rapid job growth
Wind and solar are the fastest-growing power sources, making up 62% of new power generation investments in 2018. The U.S. Energy Information Administration says that utility-scale solar will grow by 10% to 17%. As more photovoltaic systems come online and older systems age, the demand for technicians to operate and maintain them grows. In turn, increasing the need for tools and technology required for installation, commissioning, fault detection, and maintenance.
Kevin Clark, CMRP, was the Vice President of Fluke Reliability. He has more than 25 years of experience in operations leadership. His focus is on engineering, asset management, IT, supply, manufacturing automation, and safety systems.