Ask a Fluke Expert: Why Should I Use Vibration Monitoring?
Vibration monitoring is one of the most effective ways to detect and prevent equipment failure or downtime. It can screen most faults including imbalance, misalignment, looseness, and late-stage bearing wear, providing precipitous warning of impending failure.
What is Vibration Monitoring?
Put simply, vibration monitoring is a maintenance technique using vibration sensors and cloud-based software to identify frequency peaks and valleys in machine components. Vibration measurements often reveal common faults or potential downtime.
You can track the severity of these four common faults over time. Severity codes are based on data taken and analyzed from hundreds of thousands of machines by vibration experts for decades. To that end, professional knowledge and experience are incorporated into rule-based algorithms and a baseline database.
This proven process is effective on standard rotating machines, such as motors, pumps, fans, compressors, blowers, and single-shaft spindles.
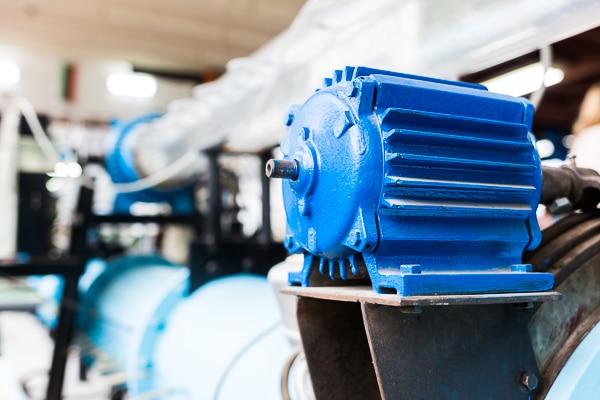
How is Vibration Monitoring Done?
Performing vibration analysis is complex. Handheld vibration meters or testers are often used for scheduled routes. Moreover, users typically require special training or hire third-party experts. Vibration analysis might be too expensive to use on most assets.
Vibration monitoring is a condition monitoring method that’s more flexible (see Figure 1) with continuous remote, wireless sensors. Monitoring assets with remote sensors is a cost-effective, scalable way to extend coverage. For instance, assets in difficult-to-reach or hazardous locations are ideal for condition monitoring. Lastly, vibration monitoring is not an alternative to diagnosing, it’s merely a way to identify that a problem exists and needs diagnosis.
(Read more below image.)
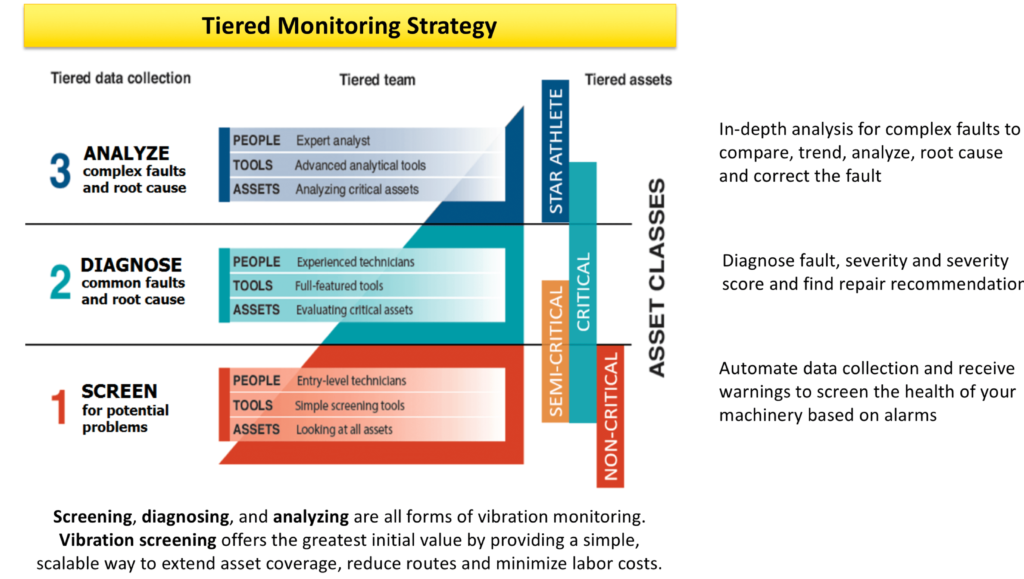
Reliability engineers, maintenance managers, and maintenance technicians use vibration sensors to preserve asset health. Installing a vibration sensor on an asset allows you to spend less time taking manual measurements. In addition, you will have more time to address problems that could lead to downtime or equipment failure.
What is the Goal of Vibration Monitoring?
Above all, identifying machine problems is the goal. Vibration screening identifies issues resulting from imbalance, looseness, misalignment, and late-stage bearing wear. However, the benefits of a predictive maintenance program go well beyond the asset lifecycle. For instance, empower your teams to:
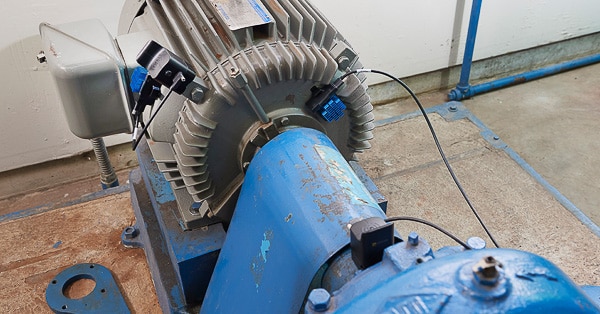
- Collect and analyze cloud-based vibration data
- Find and correct failures, earlier
- Avoid unexpected downtime
- Collect historical data to justify maintenance spend
- Democratize vibration expertise for nonexperts, providing easy-to-interpret data
In conclusion, you can increase reliability and transparency between teams using vibration sensor technology. In other words, use a CMMS with condition monitoring to receive actionable data and determine when further analysis or intervention is required. Repair can include relubrication, repairs, or replacements.
The new Fluke Reliability 3563 Vibration Screening Sensors are a perfect way to improve your predictive maintenance program.