What is Preventive Maintenance?
Preventive maintenance (PM), sometimes called preventative maintenance, is regularly performed on equipment, reducing the likelihood of failure. PMs ensure that anything of value to your organization receives consistent maintenance to avoid unexpected breakdowns and costly disruptions.
In the same way, drivers don’t wait to get an oil change until after the engine has failed. Machines, equipment, buildings, and anything of value to your organization needs consistent maintenance to avoid breakdowns and costly disruptions.

Organizations perform preventive maintenance while the equipment is operating normally. Planning “PMs,” as maintenance professionals put it, avoids the consequences of unexpected breakdowns, such as increased costs or downtime.
Preventive maintenance is a strategy that all companies can implement. Preventive maintenance moves teams away from reactive maintenance modes and begins a reliability-centered maintenance journey. The best programs include a combination of maintenance approaches. Implementing preventive maintenance is an essential step to the ideal predictive maintenance strategy.
Preventive Maintenance Benefits
With an effective preventive maintenance program, organizations see benefits to their overall business processes and costs, including increased productivity, decreased waste, improved work execution, and reduce unexpected breakdowns. A preventive maintenance program (with the support of a CMMS and other tools) can help spark quantifiable results, such as:
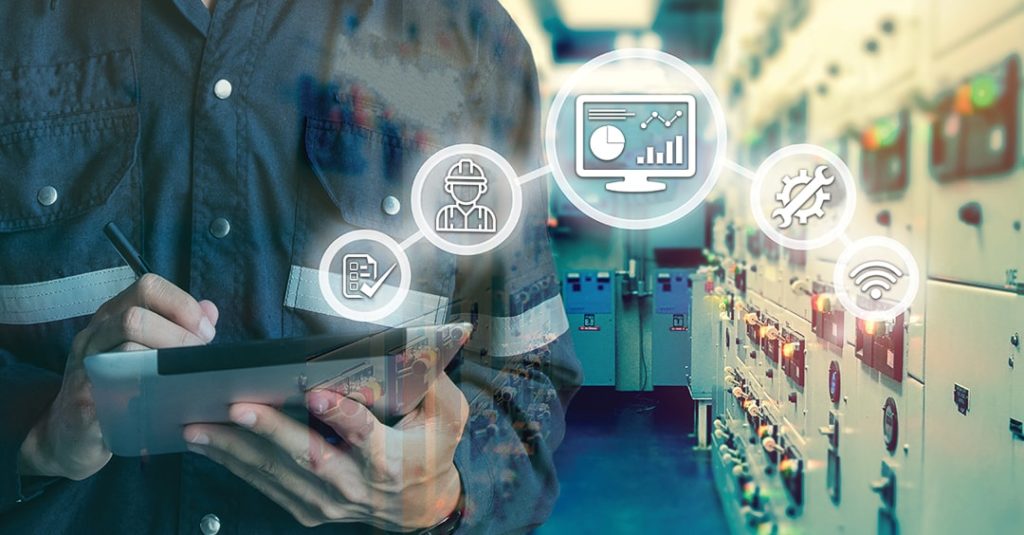
- Extending the life of assets, and increasing equipment up time
- Reducing manual data entry
- Decreasing paperwork with mobile maintenance capability
- Increasing productivity and efficiency
- Improving audit compliance with extensive documentation
Other than reactive maintenance, preventive maintenance is the most straightforward maintenance strategy to implement and execute. Teams following manufacturer recommendations develop a static maintenance schedule for critical equipment. Organizations avoid unplanned breakdowns, lost production, and equipment and labor downtime. It also decreases the cost of maintenance.
Disadvantages of Preventive Maintenance
A common issue organizations run into with preventive maintenance schedules is performing improper maintenance on assets. Because calendar-based maintenance does not take the health of an asset into account, the frequency of maintenance work can often be too high or too low. Teams prevent asset health degradation by optimizing and improving preventive maintenance programs.
Does Preventive Maintenance Make Sense for Your Business?
Many organizations are moving toward “World-Class Maintenance” status. Organizations want 90% of maintenance to be planned. Managers leveraging an 80/20 split between planned and unplanned maintenance are considered well-organized. Comparatively, operations typically average 55% planned maintenance or less. But in some instances, it makes more sense to leverage reactive maintenance.
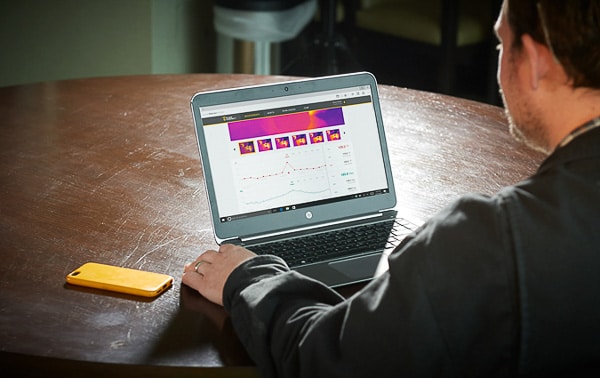
Both methods have a place in your maintenance plan. In some cases, it makes more sense to depend on reactive maintenance rather than following a strict preventive maintenance program. For example, changing a light bulb is cheap, easy to perform, and does not disrupt business processes.
To determine which maintenance strategy to apply, consider these questions:
- Is the asset critical to business operations?
- Does it contribute to the safety of your product/customers/staff/etc.?
- Is business disrupted significantly if the asset unexpectedly goes down?
- Are asset repairs or replacement costly?
If you answered “yes” to any of these questions, it is essential to begin developing a preventive maintenance schedule on that asset, as it will benefit you in the long run.
Applications of Preventive Maintenance
There are many applications of preventive maintenance in a wide variety of industries, such as:
- Performing calendar-based maintenance on air conditioning units on a university campus
- Scheduling consistent maintenance on assets critical for production
- Meter-based PMs for maintenance of material handling equipment based on utilization
- Scheduling PM tasks in preparation for audits
Sign up to speak with one of our friendly and dedicated Customer Success Managers about improving your preventive maintenance program today.