Combining Reliability-Centered Maintenance and Root Cause Analysis into one winning strategy
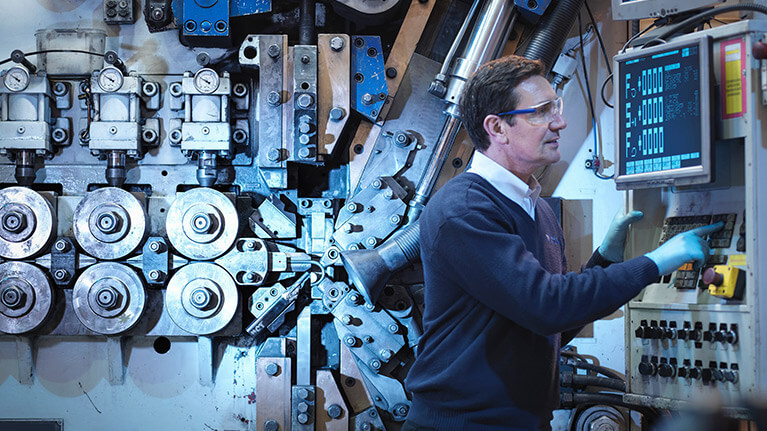
Are you approaching Root Cause Analysis (RCA) and Reliability-Centered Maintenance (RCM) as separate practices? If yes, consider uniting them. Both methodologies strongly support uptime and safety goals and are excellent ways to preserve failure mode indicators and other asset-specific information from across the team.
This perspective comes from reliability experts Doug Plucknette of RCM Blitz and Mark Galley of ThinkReliabilty, who presented on “How Reliability-Centered Maintenance and Root Cause Analysis work together to solve problems” as part of the Fluke Accelix Best Practices Webinar series. To get the full benefit of their advice, watch the recorded webinar on Accelix.com.
Plucknette and Galley position RCA and RCM as two sides of the same reliability coin. RCA is used to analyze a problem that has already occurred, while RCM uses maintenance strategies to prevent asset failures. Both practices revolve around asset failure modes and, as Plucknette says, they “train the team to ask WHY, instead of simply replacing components.”
You start by establishing your organization’s north star: operational goals. What are the team’s priorities? Why is it a problem when a machine goes down unexpectedly? If uptime or safety is the No. 1 priority, then that will help identify critical assets and weigh the impact of failure.
From there, start asking questions.
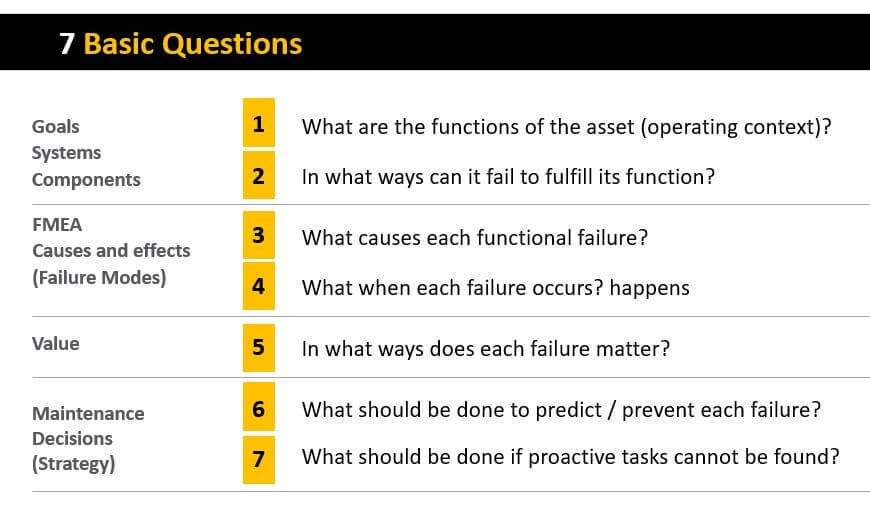
Figure 1: Seven basic questions to ask to help orient maintenance practices around RCM and RCA principles.
If you’re embarking on an RCM revamp of your maintenance processes, it’s important to think systematically about your assets. As Figure 1 describes, consider the function of your assets and how they impact the overall system. Plucknette recommends asking not just Why a problem occurs but When and Where, as well as How that problem affects the overall operations goal. Asking those questions is the first step to identifying root cause.
Galley encourages us to then map the entire root cause. Check out Figure 2. Traditionally, you would start at the left with the red box referencing asset failure and ask, “Why did it fail?” And with each “because” answer, you would then ask, “Why did that happen?” until you reach a definitive root cause. In that RCA methodology, you should then have enough evidence to make a recommendation for how to change practices to prevent the problem from recurring.

Figure 2. Traditional root cause analysis (left) vs cumulative cause mapping (right).
However, Galley says, many problems are multifaceted. There may also be several different ways (at different cost points) to solve the problem. That’s where the right-hand side of Figure 2 comes in. In the recorded webinar, Galley provides examples of how to broaden the simplistic straight line of “Why?” into a branching method that paints a more system-level picture of problems and causes. More than likely, you are facing multiple problems and multiple causes. At that point, return to your organization’s north star goal to help prioritize the resolution.
If you are using RCA and RCM together, each of these RCA problem-resolution exercises gets folded into a much larger RCM root-cause map. Both Plucknette and Galley recommend tapping the minds of the full team to document as many failure modes as possible and then practice using the mapping method as a team.
In fact, during the webinar, Galley demonstrates a very simple Excel tool for creating root cause maps for both RCA and RCM purposes. He and Plucknette also share advice for how to get started with RCA and RCM, how to train the team, and how to keep momentum going.
RCA and RCM are not competing strategies, but complementary ones. The better you get at using RCA and RCM to support each other, the better visibility and alignment you and the team will have into your overall reliability approach. To access the presentation deck and other resources used in the webinar, please visit https://bit.ly/RCM-RCA.