How to Use Failure Modes and Effects Analysis (FMEA)
In this Fluke Reliability webinar, Nancy Regan shows how teams can avoid common pitfalls when executing Failure Modes and Effects Analysis (FMEA) and making maintenance decisions. Regan is the author of “The RCM Solution,” founder of RCM Training Online, and has more than 24 years of hands-on experience facilitating RCM analyses.
Regan starts the hour-long presentation by telling the audience that fancy equipment isn’t what makes her vlog successful. Her YouTube channel thrives because she has a solid foundation of content tailored for her maintenance audience. And FMEA is much like that. It’s a foundation for proper maintenance and reliability.
What is FMEA?
FMEA is the process of reviewing as many components, assemblies, and subsystems as possible to identify potential failure modes in a system or asset, along with their causes and effects. A “Failure Mode” is what specifically caused a failure. The terms “Failure Mode” and “Failure Causes” are interchangeable. The “Effects Analysis” part is a study of the consequences of the failure.
When done properly, Regan says FMEA helps organizations define equipment goals, identify what could cause reliability to suffer, and assign criticality. FMEA can set the foundation for a reliability program, letting you get the reliability you need from equipment. Regan’s webinar began with an informal poll to discover attendees’ biggest challenges in reliability. The responses were:
- Poor reliability culture: 36%
- Lack of management support: 17%
- Lack of funding: 7%
The largest challenge: being too busy in reactive mode to work on proactive strategies. However, FMEA addresses all of these challenges.
What is Reliability?
Reliability is machine capacity and availability but that’s not the full extent. Regan believes “reliability” is designed in two ways: Literally and Figuratively.
In the literal sense, reliability is what the machine can do. And getting more out of a machine than it was designed to give isn’t going to improve reliability — that’s its inherent reliability. The machine’s capacity is what it is. Inherent reliability isn’t how long a machine will last without a failure, its’ how long it will last with proper maintenance actions.
As a responsible custodian, that’s when the figurative reliability design comes into place. Maintenance teams must ensure that machines are properly taken care of to get what they need from them. Once you take control of this equipment, there are numerous ways to extend its life.
- Proactive maintenance
- Training procedures
- Safety programs
- Supply chain analysis
- And more…
The quality of your choices and actions with machines will dictate the kind of reliability you get in return.
“Failure modes are the currency of physical asset management,” the late Reliability Centered Maintenance expert John Moubray liked to say that.
It’s in how these choices work synergistically that a machine (or operation) becomes truly reliable. And so, it’s important to start with FMEA.
4 Steps of FMEA
FMEA consists of four components: functions, functional failures, failure modes, and failure effects. Moubray also said that “Reliability isn’t a thing on its own, but rather reliability is sprinkled among all the functions of a piece of equipment.”
If you don’t know what you need from your equipment, you can’t define its reliability.
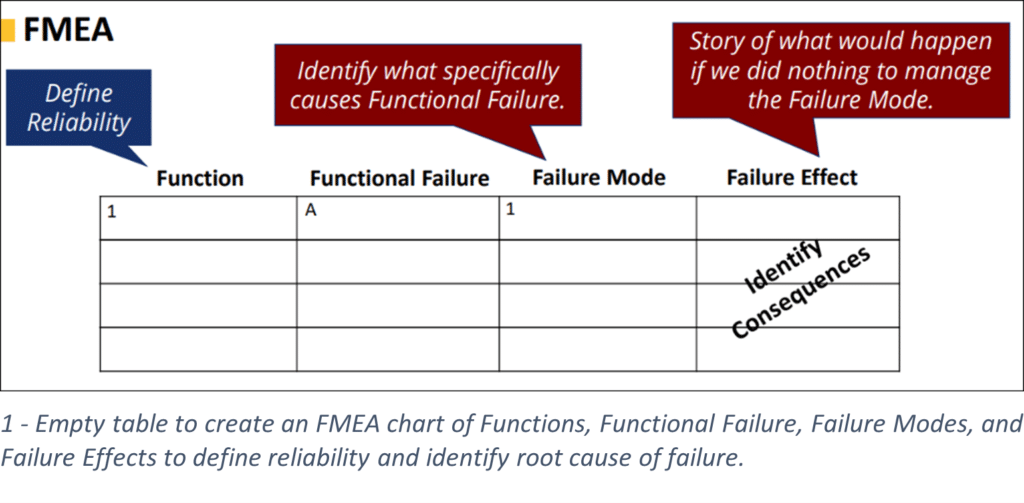
The first step of FMEA is to identify what you need from your equipment. What is its function? What does it do for the organization and operations?
The second step is to identify what functional failure looks like. As figure 2 illustrates, a functional failure of the compressor means its simply unable to provide the air needed for functionality.
The cause of that functional failure is the Failure Mode and our third step. What is causing functional failure? What’s stopping the machine from functioning properly? A Failure Mode must be written at an itemized and detailed level so that you can develop an appropriate management strategy. In the example shown, lubrication dissipating from the main drive shaft is the Failure Mode.
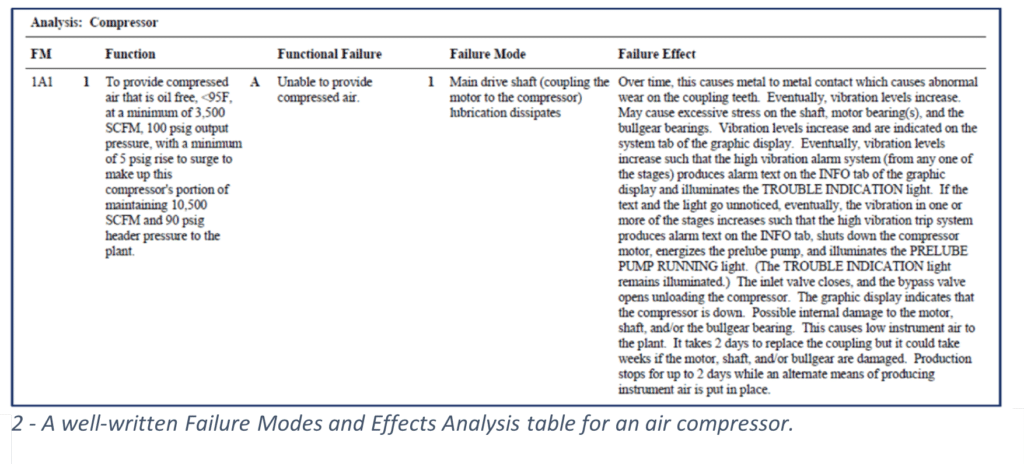
Fourth, the effects of the failure help you define a machine’s needed reliability. Will it cause a decrease in production or an increase in repair costs? Will the vibration within the machine increase to the point that it prematurely wears bearings or breaks components?
Three Pitfalls of FMEA
1. FMEA Foundation is Function
One of the most common causes of chronic failure stems from organizations trying to get a machine to do something it wasn’t designed to do. A function is not what the OEM designed the machine to do, it’s what the organization needs it to do. Writing a proper function in FMEA analysis will help teams discover what the organization needs the machine to do within operations. This is important for several reasons.
2. FMEA separate from team
FMEA actions are taken on by an individual or only part of the reliability team, like systems or design engineers. But everyone should be involved in FMEA because reliability is everyone’s responsibility.
3. FMEA not carried out properly
FMEA takes time to create, but that time pays off with improved maintenance.
FMEA leads to Reliability Centered Maintenance
As Regan nears the end of her presentation, she brings it back full circle by tying FMEA back into the reliability of assets. “When you’re doing RCM, you’re already doing FMEA,” she says.
The first four steps of the Reliability Centered Maintenance Process are an FMEA, as seen in fig. 3, with the last three being Failure Consequences, Proactive Maintenance and Intervals, and Default Strategies.
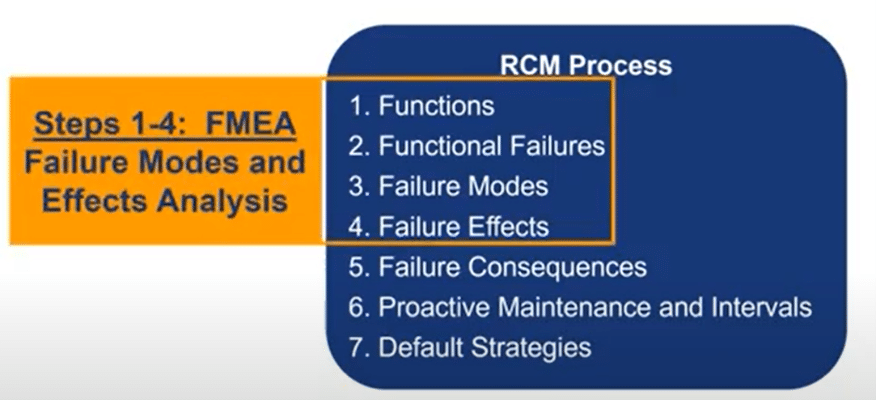
Tune in to the recorded webinar to hear more specifics about using FEMA as part of a robust reliability program.