Kickstarting condition-based maintenance with a Connected Reliability Assessment
Just like every facility is different, every maintenance operations team faces different challenges in reaching their next equipment reliability goal. One obstacle in particular is more common these days, however. With the current pressures facing plant operations, many teams would like to start using digitalized condition monitoring or connected sensors on the Industrial Internet of Things (IIoT) to more precisely gauge when critical assets need maintenance or to identify the first stages of a failure mode. What’s missing is the prioritized plan and business rationale to move forward.
An onsite Connected Reliability Assessment (CRA) is a service offered by Fluke Reliability for assessing the current state of a facility’s asset management strategy and identifying the best path forward for using condition monitoring and condition-based maintenance (CBM) to improve asset reliability. The service applies equally well for sites that have never implemented CBM as well as for sites that have tried it unsuccessfully and want to revamp or restructure their efforts.
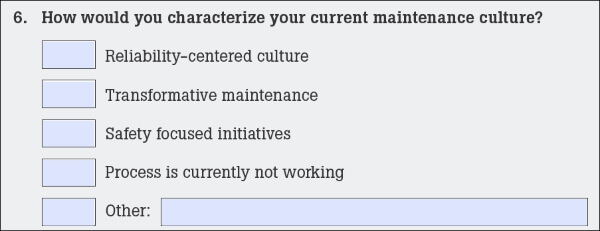
The CRA begins with a pre-visit questionnaire to help Fluke better understand the team’s current asset maintenance situation. That information helps the CRA service providers prepare a plan for their on-site visit.
At the start of the two-day assessment, a Fluke reliability expert holds a kickoff meeting with the plant’s key reliability stakeholders to confirm the desired optimal state. Then, Fluke conducts an in-depth review of the plants’ current operational state, from energy sources to networks, assets, mobility capabilities, training and skill levels and tools used.
The outcome is a comprehensive report of findings, recommendations, and a roadmap of next steps. Like the CRA itself, the report is highly customized to the customer’s organization, their current situation, and their near- and long-term reliability goals. The report describes the level of connected reliability that makes sense based on the plant’s asset health goals, recommends a starting point, and advises what data, systems and teams to connect. Experts from the CRA team remain available for follow up questions after the on-site visit.
For more information about the connected reliability assessment, visit fluke.com
Related articles:
Connected Reliability Assessment
How to connect a facility even when the customer is skeptical