How machine alignment impacts maintenance strategies
Much of the work tied to machine alignment is standardized. But what happens after the alignment? There aren’t formal standards for what comes next, yet the strategies you adopt after alignment can help extend equipment lifespan.
The presenters for Fluke Reliability’s Sept. 18 webinar titled “What happens after the alignment” are experts in asset maintenance and operational engineering. Michael Ciocys is a technical service & support manager at Fluke Reliability’s Prüftechnik arm, with a mechanical engineering degree from Temple University and CAT III certification for Vibration Analysis and Condition Monitoring. Chelsea Fiegel is Prüftechnik’s Service Sales Leader for North America with an environmental engineering degree from Penn State. Both brought a slew of expertise and advice to help teams reach their alignment goals.
At the beginning of the webinar, they asked attendees, “After aligning new equipment before start-up, have plans been made to monitor assets?” Many suggested that they would be monitoring equipment with vibration routes or screening technologies (62%). Several also indicated they would only do it on critical machines (17%) or weren’t even making plans but do something completely different (15%).
Why Align Machines?
Pre-start-up alignment provides a machine baseline from which all other measurements and performance statistics can be compared. That requires teams to plan for monitoring and trending parameters, interpret asset health data, and strategize recurring service elements to maintain and sustain asset conditions.
Different Kinds of Machine Alignment
- Shafts need collinear alignment — a straight line through three or more points
- Cylinders need parallelism — two or more lines with the same direction and angle
- Plates require coplanarity — or three or more non-collinear points on the same plane
There are many aspects of machine alignment, depending on what kind of equipment a maintenance team is aligning. And the machine alignment tools used in each application are different, such as plumb bob and tape measure (low precision) vs. geometric laser trackers or a roll alignment device like ParAlign (high precision) that measures all directions at once. The more accurate an initial, pre-start-up alignment, the more precise the baseline performance of a machine will be for later data analysis.
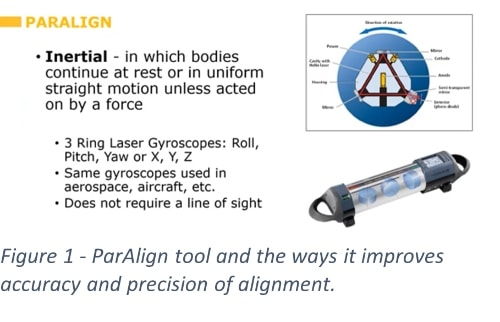
In a piece of equipment, there may be rotating shafts driving the cylinders of a conveyor roller system relative to each other and other components that needs to be aligned as a whole piece of equipment relative to the floor. This kind of job that requires all the above types of alignment.
Post-Alignment Maintenance
After alignment, whether initial or operational life cycle, the Potential-Failure (PF) Curve then takes over, with deterioration and wear occurring over time. Taking an active roll in the PF Curve allows teams to extend the asset’s lifecycle and stretching the time to potential failure.
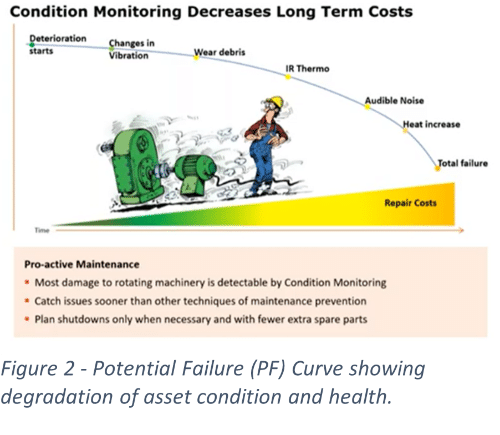
“Hopefully, you start a machine, and it runs for a very long time, but, at some point, something does happen,” Ciocys said during the webinar. “Ultimately, you’ll either repair or replace a machine.”
An inaccurate and imprecise alignment can cause wear. And its subsequent physical manifestations, like heat or vibration, will decrease equipment life. The machine would have to be either taken down or run-to-failure as the problem worsens, causing possible operational setbacks.
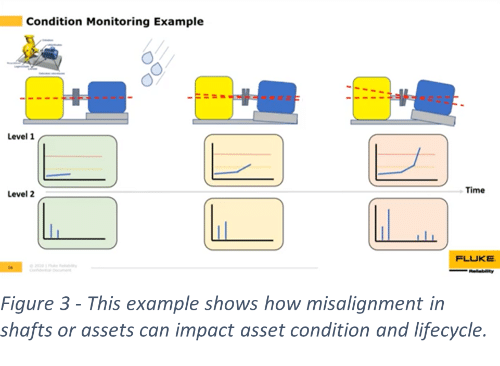
Post-Alignment Data Collection Methods
The best maintenance strategies are not one of these methods but a combination of all three that empowers teams to control and plan maintenance in a holistic, interconnected way.
Route data collection
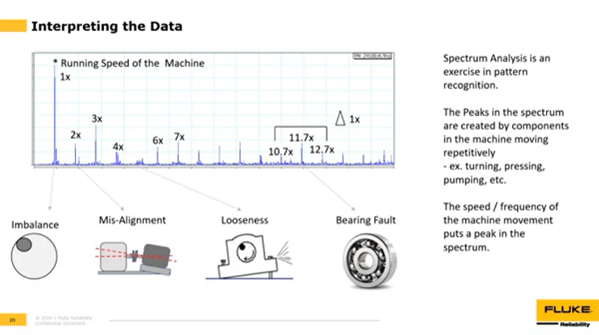
Measurements are taken at specific time sets—like monthly or quarterly—capturing a snapshot in time of asset health.
Wireless Condition Monitoring
Continuous measurements — like hourly or always-on — runs without human interaction. This technique works well for assets in harmful areas or that are critical to operations.
Online Condition Monitoring
Condition monitoring can alert users on asset conditions in real-time. Great for high-value, non-redundant, complex, and/or mission-critical assets.
With the different kinds of data, teams can start to interpret the information to make data-based decisions. A spectrum vibration analysis can determine imbalance, misalignment, looseness, or bearing failure depending on the frequency, speed, and peak intensity. This, in turn, tells teams what kind of maintenance is needed.
In-House or Outsource?
Attendees indicated that when a fault is found, and work needs to be done they:
- 58% – Handle it fully-in house
- 55% – Mix of in-house and contractors
- 24% – It’s complicated, on a case-by-case basis
- 13% – We pull in outside contractors for most work
Vibration, oil, or ultrasound analysis and testing are great ways to complete or complement a maintenance plan or services. There may be no bandwidth, funding, or resources for some teams to start an in-house effort for these kinds of condition-based maintenance data collection.
Fluke Reliability offers customized and flexible remote condition monitoring service options — by ISO Cat certified professionals — for teams, including:
- Rent/Buy options
- Data Collection: In-house or Outsourced
- Analysis: In-House or Outsourced
- Lease/Subscription model: Combination of hardware, software, and services
Fluke Reliability also offers onsite and online training on product use, data collection, and vibration analysis. Our team supports and adapts to customer needs, even down to a per-plant basis.
“For alignment, there’s a couple of ways information is portrayed,” Fiegel said of the individualized reporting from Fluke Reliability services. “For ParAlign specifically, a report is sent via corresponding software. For a laser tracker, the customer would receive a two-dimensional image of horizontal and vertical offset at the end of the service, and a follow-up report sent a few days later showing how the rolls were moved from initial to end position.”
Roll Alignment with ParAlign
Suitable for measuring roll misalignment on assets with numerous interlinked rollers, such as calendering machines in paper or steel mills.
Geometrical Measurements with Laser Tracker
Suitable for complex machines with various machine elements, such as conveyors in industrial applications.
Shaft Alignment for Rotating Assets
Suitable for measuring multiple axes of coupled shafts of various sizes and lengths, such as a motor and connected machinery.
Alignment as part of Reliability
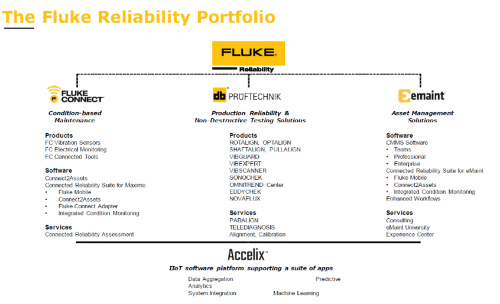
For a fully connected, reliability-centered maintenance program, the presenters advised that teams use multiple aspects of the Fluke Reliability portfolio of products, software, and service offerings. From training for in-house execution to offering tailored services that meet operational needs, all it takes is a conversation with one of our Maintenance and Reliability professionals to start taking advantage of the breadth and width of our portfolio.
Want to watch the Best Practice Webinar “What happens after the alignment” featuring Mike Ciocys and Chelsea Fiegel?