How to break habits and implement pandemic-related changes at the plant
“Virus-driven decision making.”
Dr. Klaus Blache, Director of the Reliability and Maintainability Center (RMC) at the University of Tennessee, used this phrase to begin his June 2020 webinar, “How to lead and maintain reliability in a crisis.”
“Many things have changed, and many have not in these challenging times of virus-driven decision making. (But) as reliability and maintenance activities continue, adherence to new pandemic-prompted standardized best practices is even more critical,” Blache told attendees.
Blache retired from a long career at Cadillac more than a decade ago to assume his current role in academia, where he also serves as a research professor at the University of Tennessee’s College of Engineering. In this time, he has doubled down on communicating the importance of plant culture in achieving reliability goals. In study after study, for example, Blache has shown that the best way to reduce reactive maintenance is to instill an empowered, problem-solving mindset in the entire maintenance and operations team.
Now that knowledge of how to change ingrained work habits has become as relevant as ever, as plants must alter standard workflows for COVID-19 safety practices.
Crises such as COVID-19 trigger different reactions in people, Blache noted. Some will feel uncomfortable and want to work from home. Others will take what they learn and come out better individually and as an organization.
Just about everyone, however, wishes they could return to a safe workplace. It’s best to accept, said Blache, that many things aren’t going back to the way they used to be.
“What employees will find upon their return is that virtually nothing is the same. Entering the plant is different; working processes on the assembly line are different; meetings with team leaders are different; taking breaks is different; eating lunch is different.”
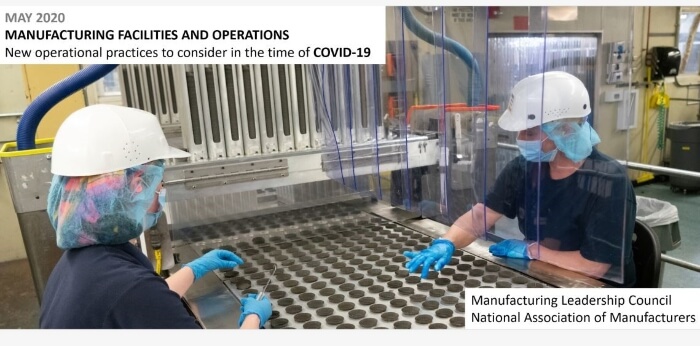
Most people don’t fare well under ongoing uncertainty, Blache noted, and are going to behave and perform differently in uncertain circumstances. Compensate the best you can with communication and training, extra time for learning new procedures, and re-writing the processes themselves to reflect the new realities, he said.
Planning new safety practices for the long term
Many agencies and groups have issued guidelines for safe work practices during the pandemic. Most important are those from the Centers for Disease Control & Prevention (CDC), the Occupational Safety & Health Administration (OSHA), state departments of health, and other industry-specific regulations. Watch Blache’s full presentation for an extensive list of newly-created industry-standard best practices for pandemic environments.
In particular, OSHA on May 19, 2020, issued revised guidelines that emphasize the importance of record-keeping. Employers will be expected to investigate COVID-19 cases just as they would any other illness case.
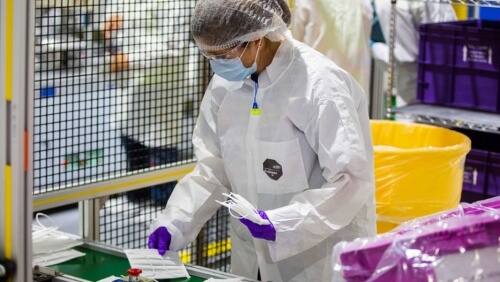
Some of these measures may be short-term solutions, but Blache advises planning for the long term. Our new normal, he said, involves becoming resilient. We will need to sustain these changes long after the urgency fades, and that requires creating lasting habits.
“There will be hiccups, because of global supply chain issues and other unforeseen complications, but you have to start. Effective startups require detailed understanding, teaching, coaching, and patience from everyone.”
For the first time in modern manufacturing history, Blache said, demand, supply, and workforce availability are affected globally at the same time.
Implementing change that is sustainable
So how do we adapt? He offers five guiding words to describe what’s needed. Remember them as the five Rs:
- Resolve: Rethink business models to be sustainably profitable
- Resilience: What happens in the next three to four months will be critical
- Return: What is our path to rehiring, training, and achieving previous levels of productivity?
- Reimagination: We will never look at supply chain availability the same way again
- Reform: Contingency production for critical supplies
In particular, Blache stresses that:
- The weakest link in the chain, such as staff objecting to new procedures, can hold everything back.
- Historically in manufacturing, we are not good at instilling daily best practices. Most people will follow the COVID best practices initially because of personal risk, but how good will we be at sustaining that?
- Supply chain safety and availability are more important than cost.
- People are good at problem-solving. Utilize the Kaizen mindset and encourage the continuous improvement mindset.
- Flexible companies do better in a crisis.
- Sustainment requires a change model; to get people to buy-in, they must understand the “why” of the situation.
View Blache’s full presentation on replay to learn more about these strategies.