The new, post-pandemic world of maintenance and reliability
Reliability professionals such as Ramesh Gulati, a recognized expert in the field, have experienced one of the most dramatic slowdowns in the history of business and industry since the pandemic began in early 2020. Now Gulati is one of many evaluating how maintenance and reliability units can help lead their companies safely into recovery.
Gulati is an asset management and reliability specialist with Jacobs Asset Management Group in Tullahoma, Tenn., and is known in the industry as “Reliability Sherpa.” In May, Ramesh joined the Fluke Reliability Best Practice webinar series to discuss “Lessons from the pandemic to help maintenance and reliability pros be more effective.” Gulati addresses several key questions, including: How have the practices, goals, and framework of reliability engineering and maintenance been changed and what will be the norms going forward? You can listen to the replay on Accelix.com.
Accounting for the human impact
Gulati starts by addressing the human impact of the quarantine, which has many people working from home or not working at all. It is best to be aware of the stresses around us, rather than brushing them away, he advises. The impact on us is profound, even if not always obvious. He suggests taking time to note the positives, from cleaner air because of fewer cars on the road to people spending more time with family.
When it comes to our workplaces, it could be tempting to focus on just one’s M&R team, building, or industry. But Gulati encourages us to consider the broader impact of the slowdown. Failing to account for the interdependencies between regional economies, vendors and suppliers, and market dynamics and fluctuations can undermine even the best-led team.
The ‘new normal’
“We must implement new ways of doing business,” he advises. From personal safety to team, plant, and remote work processes, the considerations include:
- Updating or developing new workplace procedures: This may require extensive communication and training. Go the extra mile to make guidelines simple and easy to follow, he says, and base them on evidence over assumptions. Make data-driven decisions and consult the subject-matter experts.
- Always wearing appropriate PPE: Gulati advises taking new PPE guidelines to heart. This means updating procedures and job descriptions, maintaining sufficient PPE stock in the storeroom, and wearing correct PPE at all times. “We all have challenges in ensuring that we—all of us—wear appropriate PPE as needed for the task at hand,” he says. “We all need to become role models, especially leaders and managers.”
- Digitalizing workflows wherever possible: Protect worker safety by reducing the need for person-to-person direct interaction and encouraging physical distancing in the workplace. Also, enable more opportunity for people to perform their jobs remotely.
- Empowering more team members to think and act like knowledge workers: Videoconferencing and other communications tools will only grow in importance. Technicians and others must become more steeped in digital tools and systems.
Gulati cited the Ford Motor Co. and Volkswagen as early leaders in adjusting their workflows to account for social distancing and other COVID-19 safety practices.
Ford, for example, has issued all employees a digital band to alert them if they come closer than six feet to another person. Volkswagen has rolled out more than 100 workplace changes, including having workers pass materials by setting items down, not hand-to-hand, and requiring employees to enter factory gates in single-file lines to keep six-feet of distance at all times.
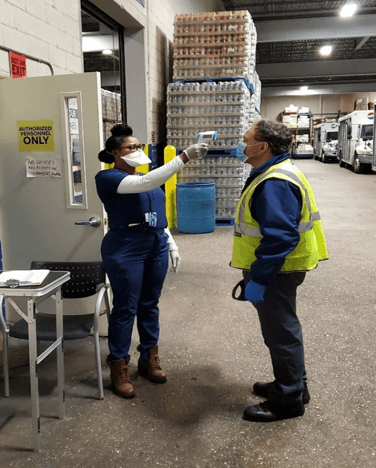
Many workplaces have instituted temperature checkpoints or employee health screenings (as demonstrated in Figure 1) and have closed down break rooms and smoking areas to prevent employees from congregating in one spot.
“The overall (change) is so exhaustive, staff will have to take extra time to absorb the new rules,” Volkswagen union officials stated in an article that Gulati referenced.
Changes to maintenance and reliability
What about changes specific to reliability engineering? What should a reliability engineer or maintenance technician expect?
Most facilities are increasing digitalization efforts and plan to do more with their EAM and CMMS platforms. Yes, many maintenance and reliability teams had already been updating and digitalizing their core systems and workflows over the last couple of years. Now, this current situation is increasing the speed of digital workflow adoption, such as:
- Leveraging more automation, especially where it can reduce the need for human interaction
- Implementing IoT sensors instead of using manual measurements for routine asset checks
- Utilizing mobile devices for teamwide sharing and communication, instead of one-to-one contact
- Reducing or eliminating printouts of work orders; use a tablet and proceed digitally
- Encouraging cross-training so that more people on the team can stand in for each other
- Working from home when possible—technicians as well as engineering and management
- Creating or updating maintenance plans for unexpected catastrophic events
Most importantly: Extending the use of technology and online learning to everyone on the team.
Accepting this degree of change is not going to be easy, especially with the ongoing degree of uncertainty we all face, Gulati notes. During the webinar, he offers coaching on how to help people accept change. “Change is here, this is the new normal. Let us accept this change, think how we can make it better, and make a plan.”