CMMS 101: Understanding Hierarchical Structures in CMMS
Engineers developed Computerized Maintenance Management System (CMMS) software to improve the management and performance of an organization’s assets. However, CMMS users must have an underlying hierarchical structure that provides a foundation for those assets. Users can set up hierarchical structures in CMMS in various ways with a few underlying principles to develop a hierarchy that works for the organization.
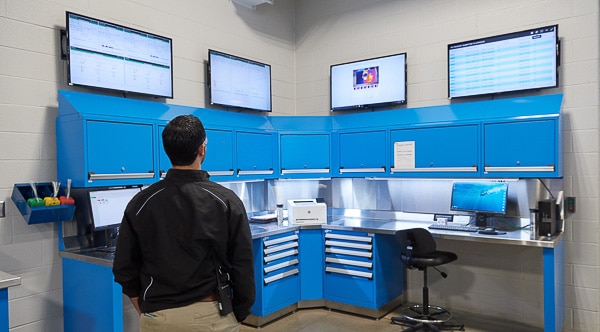
Hierarchical asset structures are not just a copy-and-paste solution. A lot of thought goes into the process. Managers must decide why hierarchical structures make sense for their organization and what connections they need to make between assets.
So now you might be asking yourself, what exactly is a hierarchical asset structure in CMMS? What are the benefits? And what is the process of developing these structures?
Asset Hierarchical Structures in CMMS
“A system in which people or things are placed in a series of levels with different importance or status.”
Miriam Webster, definition of Hierarchy
Concerning assets, hierarchy is the relationship between the highest level of equipment and subordinate parts. For example, a technician may classify a tractor two levels above its carburetor system in an equipment hierarchy. Maintenance professionals call this the “parent-child relationship.”
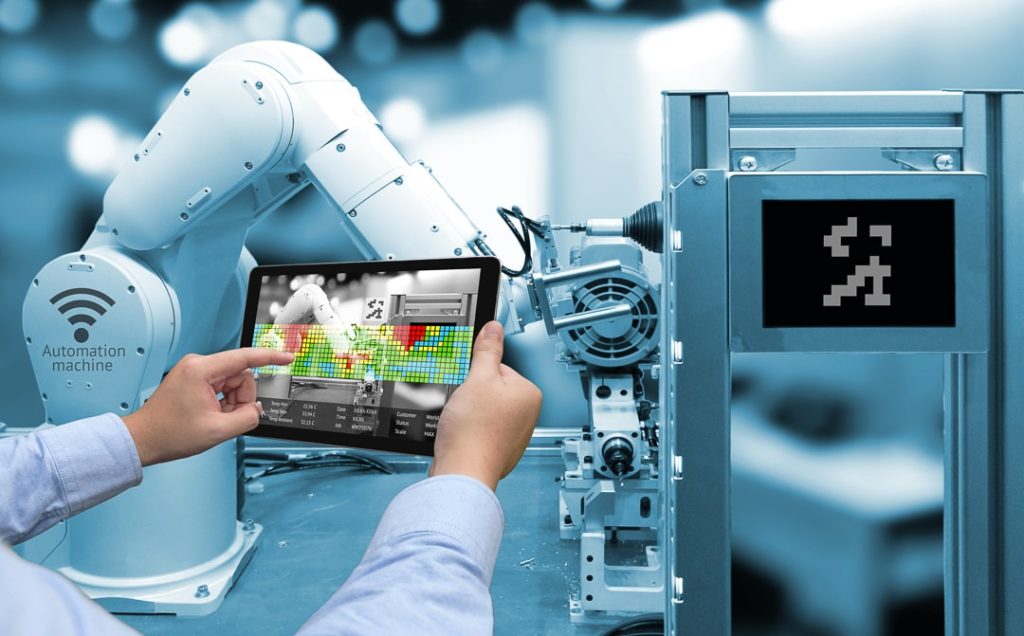
Establishing this relationship allows you to easily identify which assets you can perform maintenance and reliability on vs. all of your tangible pieces, parts, equipment, and rooms. Just remember: it’s all about how to organize your assets to maximize wrench time, productivity, and profit.
Read more: What is Enterprise Asset Management?
Benefits of Hierarchical Structures in CMMS
With the right asset hierarchy, an organization can greatly improve asset performance. You could realize improvements such as:
1. More Effective Preventive Maintenance Scheduling and Predictive Maintenance Activities
Consider your planner’s process for preventive maintenance scheduling on a piece of equipment. With a sound hierarchical asset structure, all the assets associated with that piece of equipment, such as gearboxes, instrumentation, safety valves, and isolation points, become candidates for maintenance while the equipment is offline. This is an especially salient idea to increase uptime and productivity during unplanned breakdowns. Asset hierarchies allow technicians to understand which assets have upcoming PM tasks scheduled in a matter of seconds. Then your team can perform that maintenance and take advantage of an unscheduled event, rather than racking up even more downtime for your technicians and assets.
2. Charge Costs to the Lowest Possible Asset Level
An effective hierarchical structure helps identify where maintenance dollars are actually being spent. It enables maintenance to write work orders for specific asset levels rather than to a general area. If no one sets up hierarchies, work orders could be charged to large locations such as “The Mill” or “The Kitchen.”
To understand what is actually driving these costs, you would have to pour over hundreds or thousands of work orders to crack the case. Asset Hierarchy takes this out of the equation by providing you with asset classifications upfront. This helps develop historical data that can calculate the total cost of ownership and contribute to actual data to make “repair vs. replace” decisions.
3. Hierarchical Structures in CMMS Allow for Failure Mode & Effects Analysis (FMEA)
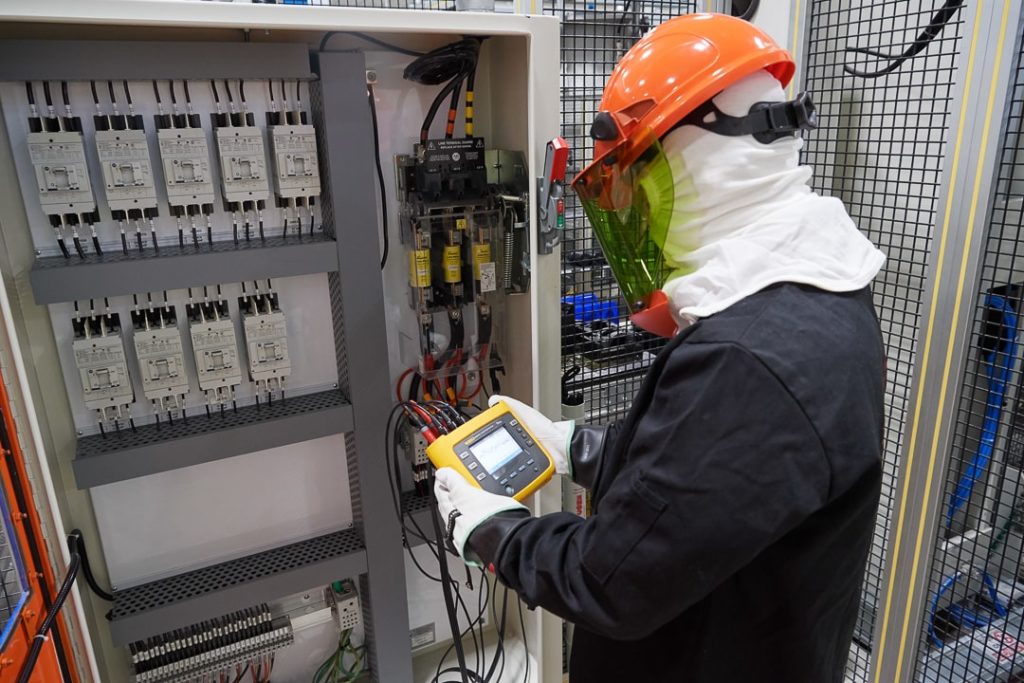
FMEA, or failure modes effects analysis, is a step-by-step approach for identifying all possible failures in a design, manufacturing process, asset, or service. “Failure Modes” are how something might fail, and “Effects Analysis” refers to studying the consequences of those failures. Failures are prioritized according to how severe their consequences are, how frequently they occur and how easily they can be detected. The purpose of the FMEA, as an extension of relationship hierarchy, is to help you take action, think maintenance plan, and eliminate or reduce failures.
Beginning a Hierarchical Asset Structure
So while this all sounds great, how do you actually begin developing an Asset Hierarchy?
1. Start with the end in mind
When setting up an asset structure, it is essential to consider what information is important to you. Considering the following questions is vital in taking initial steps in making smarter, faster, and better decisions.
- What is the total cost of ownership for a particular piece of equipment?
- Which child component is causing the most unplanned downtime?
- What is the mean time between failures for a particular equipment type?
- Which child component should be included in the next PM outage?
- What is the mean time to repair similar equipment but different manufacturers?
- What is the break even analysis for repairing vs. replacing?
2. Set up your specific asset hierarchy
Make sure your hierarchical asset structure has not just been cut and pasted from someone else, and make sure there was some thought into why it makes sense for your organization. This includes:
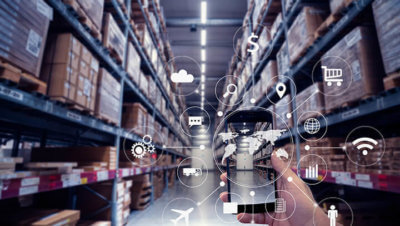
- Looking at a building diagram of your asset domain. What natural groupings do you notice? Where are your power sources? What is the natural geography that drives your decision making?
- Start identifying similar assets, assets from the same manufacturer, assets with similar power consumption ratings, etc.
- Set up Parent/Child Relationships using categories such as Asset Tag, Asset Name, Parent Asset, Parent Asset ID, Asset Type, Manufacturer, Model Number, Serial Number, Location, and Room / Level.
3. Monitor asset performance
Within a month of setting up your asset hierarchy, start running reports and getting in a room with subject matter experts. Ask them what is most important? What is the Mean Time To Repair (MTTR) assets? If you can’t answer these questions within a few keystrokes, you have probably missed something in your hierarchy. It’s time to go back and fix it and rework your structure.
4. Prioritize improvement areas
Use Root Cause Analysis (RCA) to root down to see driving costs and do an FMEA exercise. Though the FMEA seems to be a tedious process, you will be surprised about the level of brainstorming and evidence for decision-making this data can enable.
Conclusion
Utilizing an effective hierarchical structure can completely revitalize the management and performance of your organization’s assets. Establishing parent-child relationships between your assets is a vital aspect of this structure. In seconds, you can discover which assets have PMs coming up and perform all of this maintenance simultaneously – even during unscheduled shutdowns.
Hierarchical Asset Structures are a process and take a lot of work to flesh out. Once your organization begins to see results from the relationships you construct, new levels of communication can develop. With meaningful data about assets to help drive repair vs. replace decisions and a way to group equipment PMs to help make the most of your time, your asset organization and management may skyrocket.
Learn more about Asset Criticality Analysis and how eMaint can help.