Maintenance Planning & Scheduling, CMMS Benefits
To achieve world-class performance, organizations must plan, schedule, and track maintenance activities. Maintenance planning and scheduling are two different functions that work together to create a maintenance program. As it sounds, maintenance planning is the process of planning, while maintenance scheduling is the process of reconfiguring workloads in a production/manufacturing process. Maintenance scheduling is used to allocate plant and machinery resources, plan human resources, plan production processes, and purchase materials.
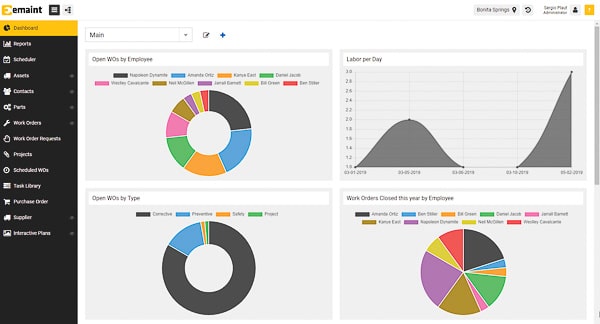
Computerized Maintenance Management Systems (CMMS) offer the tools to plan and schedule maintenance, measure what you treasure, and act on the results. However, a successful implementation process is critical to leverage the full power of a maintenance management system. There are three main elements that are associated with a CMMS implementation journey:
- Continuous improvement
- CMMS building blocks, including assets, PMs, contacts, parts, work orders, and schedules
- Asset Reliability Strategies or best practices such as ISO 55000, ISO 14224, KPIs, MRO, TPM, and RCM
Having the Right CMMS Implementation Team
Establishing a CMMS implementation team helps facilitate success prior to implementing software. Select your team from a cross-functional array of internal team members. Members may come from a variety of departments including maintenance, IT, materials management, and more.
The maintenance planner/scheduler is a critical role to fill. Maintenance planners manage your work backlog and resources in alignment with maintenance projects to complete. The maintenance planner/scheduler also develops practical and innovative ways to identify and meet goals.
In a day in the life of a maintenance technician without a properly implemented CMMS, what is happening and where is the time going?
- 22% hunting parts
- 21% wrench time
- 15% waiting on associates
- 13% looking for tools
- 12% waiting on equipment
- 5% waiting on permits
- 3% waiting on supervision
Building a world-class maintenance program
“World-class” maintenance statistics, best practices, and concepts set the standard for global organizations. The world-class concept was first introduced in the automobile and steel industries, pioneered by Japanese manufacturing organizations. Organizations that strive to adopt world-class manufacturing often experience higher productivity, lower costs, and higher quality output.
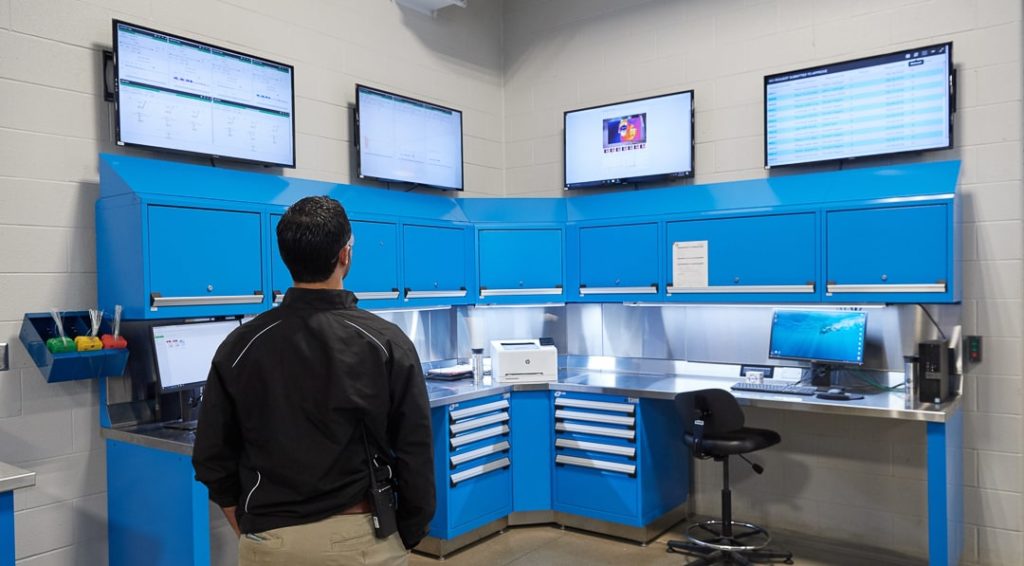
In a recent poll, 32% of respondents explained that they perform maintenance planning and maintenance scheduling activities, but their processes are not formalized, and 22% said that they’re performing reactive maintenance. By developing standardized processes and avoiding reactive maintenance, wrench time that is currently 20-35% direct work (not hunting for parts, information, or waiting for equipment to become available) becomes “world-class” maintenance with 55% direct work and a 57% improvement. So, the work of 20 technicians can yield the “world-class” maintenance equivalent of 47 technicians with a 57% improvement.
Maintenance Planning Principles
Maintenance Planning Principle #1
It is very important that the role of the maintenance planner/scheduler is identified to be independent of the other activities going on within a plant or facility. Taking planners off the tools and putting them behind a desk lets them concentrate on the administration of work being done. Responsibilities of the maintenance planner/scheduler should not include:
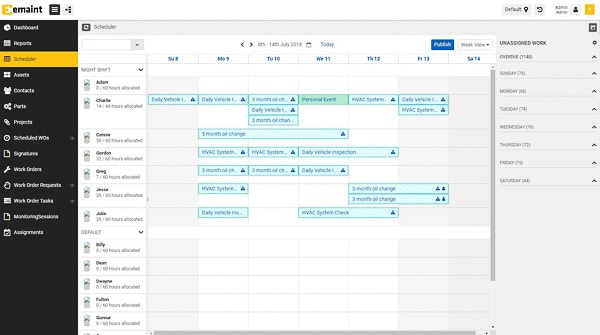
- Planning emergency work
- Acting as a relief supervisor
- Becoming a material expeditor
- Working on tools
- Performing time-consuming clerical activities
- Becoming a “go-fer” for maintenance / operations supervisor
Maintenance Planning Principle #2
A maintenance planner must focus on arranging current and future preventive maintenance work, as well as allocating the appropriate resources, parts, finances, costs, and reliability information for each project. The planners must also emphasize constant improvement, and use the Deming model on continuous improvement for planning, doing, checking, and acting/adjusting schedules:
- Problem
- Goal
- Point of cause
- Root causes
- Counter measures
- Follow-up
- Standardization
Planning principle #3
When implementing different component levels within your CMMS, take advantage of International Standards such as ISO 14224 for best practice tips and ease of compliance. Component levels are “minifiles” on every piece of equipment. They include work order histories, equipment registry, parts registry, and more.
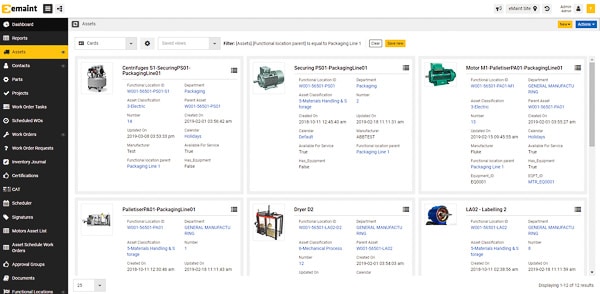
Maintenance Planning Principle #4
Once you identify tasks, an important principle of maintenance planning is to ensure all instructions are documented and standardized. The best planners have experience estimating time and comparing actuals of work done in bite-size chunks in order to bring efficiencies into the next iteration of carrying out preventive maintenance.
Maintenance Planning Principle #5
Sometimes it’s not best to reinvent the wheel for all pieces of equipment. Maintenance planners should take advantage of standard plans and enhance them. Plans will also take into account and recognize the skills of craft technicians.
Maintenance Planning Principle #6
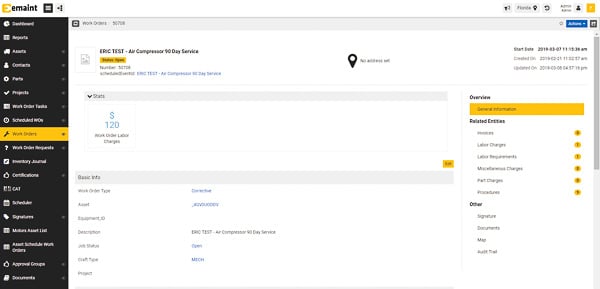
Take advantage of data from past work to properly estimate appropriate and accurate plans for the future. This will make wrench time more available and the more wrench time available, the more maintenance activity can be performed.
- Measuring how much time craft technicians actually spend on the job site versus other activities determines the effectiveness of the maintenance planning program: (Obtaining parts or tools, etc.)
- Avoid delays, as they are not part of your job
- Use sample wrench time to measure how effective planning can be
- Metrics determine how effective your maintenance team is and look for ways to improve performance when gaps emerge
People Rules of Maintenance Planning
- The maintenance planning program is not trying to give away the plant’s work to contractors
- Planners cannot do the perfect job
- Planning is not designed to take the brains out of your technicians
- The technician owns the job after the supervisor assigns it to them
- Planners cannot make the perfect time estimate
- Management cannot hold technicians accountable to time estimates for single jobs
- Showing what is not correct is often as important as showing what is correct
- Planners do not add value if they help jobs-in-progress
- Everyone is an adult
- People should enjoy their work
- Employees should go home at the end of each day knowing if they have won or lost
- Wrench time is not strictly under the control of the technicians
- Schedule compliance is not strictly under the control of the new supervisors
- It is better to train employees and lose them, than not to train them and keep them.
Maintenance Scheduling Principles
Maintenance Scheduling Principle #1
You should set realistic goals and schedules. The planner/scheduler must look at the appropriate resources for the work to be performed, estimating the hours and effort it will require. To manage this process and avoid roadblocks, try to plan to the lowest required skill level available and work upwards.
If you work the opposite way, organizations may end up in a situation where skills are available, but the sort of work available is not appropriate for the priority level skill element. As a best practice, at the beginning of a project, identify skills for:
- # Persons
- # Work hours
- Duration of work
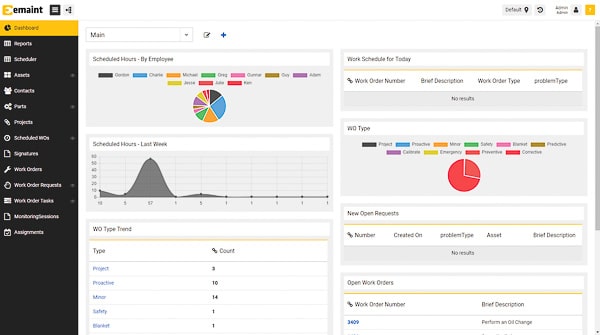
Maintenance Scheduling Principle #2
For the most effective work scheduling, identifying job priorities is important. Your highest priority work (Priority 5) is the most urgent and should be followed up on first. For example:
The ISO 14224 standard can help prioritize activities with the Failure-consequence Classification chart. It is useful in terms of setting up asset information, analyzing reliability information, putting P&ID or boundary drawings together, etc. It helps in terms of how to prioritize one work order over another.
Maintenance Scheduling Principle #3
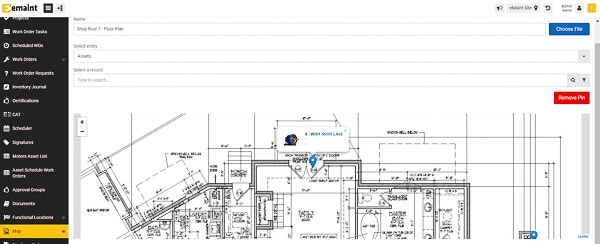
Scheduling from forecasts of the highest skills available helps to increase productivity. If the work orders are generated 10 days in advance, then more details can be put into the scheduling, resources, availability of parts, and work to be done. Consider what jobs can be put together, what jobs can be grouped, what condition monitoring work is outstanding and can be bundled, and any proactive work that can be done in advance.
Maintenance Scheduling Principle #4
To help set up an organization’s maintenance team for success, scheduling work for every hour available is a good rule of thumb and allows for organizations to achieve practical goals.
In March 2015 on the Maintenance Planner / Schedulers group on LinkedIn, a member asked:
“Normally scheduling is 100% of available resources. Due to several reasons assigned works are completed earlier than the planned time. In order to increase craft utilization (wrench time) should we increase the scheduling % of resources?”
An answer to this question comes from Doc Palmer, author of McGraw Hill Maintenance Planning and Scheduling Handbook:
“The purpose of the schedule is to help us complete more work than we would normally do without the schedule. My experience is that crews that start out with a 100% loaded schedule complete more work orders than crews that start out with only 80% loaded schedules. The crews that start out with 100% loaded schedules do have lower schedule compliance. The schedule compliance score is a management indication of how much is in the way of the crews trying to complete expected work.”
Maintenance Scheduling Principle #5
When it comes down to daily activities, the planner/scheduler should leave the granular detail to a crew leader or technician supervisor. With proper training, these crew members can use a CMMS and take advantage of functionality to realign the resources based on their priorities for the day. This should be easy enough if the planning and scheduling are proactive. However, know that potential emergencies and urgent activities might interrupt the day. There is still a chance that it can be done if 80-90% of the day is planned out.
Maintenance Scheduling Principle #6
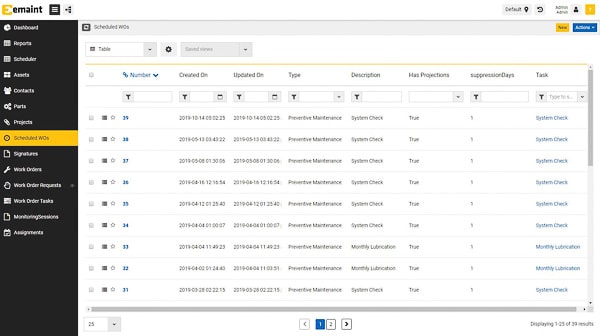
In order to keep employees engaged, begin measuring performance by analysis of scheduled success. This measure avoids supervisors feeling the calculation gives an unfair poorer-than-actual view of their performance and offers the crew any benefit of any doubt.
- Schedule 80-90% of maintenance
- Planned by experienced technicians
- Processed as a backlog, weekly schedule, then daily work
- Must be flexible enough to accommodate emergency work
- Don’t schedule maintenance until ready
Maintenance Scheduling Principles Summary
If your organization is failing to plan, then you’re planning to fail. Maintenance planning and scheduling is a systematic approach to optimize efficiencies while maximizing work performance and is the most critical element to ensuring proactive maintenance.
Let Fluke Reliability show you how eMaint CMMS can improve your Maintenance planning and scheduling.